RIPPING OFF THE EIFS
To rip off or not to rip off; (EIFS that is) that is the million dollar question. The answer is uncomplicated, and applies to practically all types of cladding. For starters, you must go beyond the symptoms of water intrusion problems, and find the actual sources of the leaks. After all, a constant drip on your forehead should be all the proof you need that you need help. As a professional EIFS contractor and EIFS consultant, I have seen it all. Most EIFS problems occur in residential construction due to a lack of quality control initiatives in the field. EIFS is not a cladding the average homeowner can repair, but many EIFS repair contractors have been trained in the repair through manufacturers. Before you hire any so-called EIFS expert remember to do your homework and ask for references.
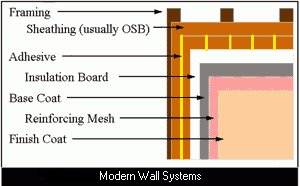
Let’s start with the basic facts about EIFS cladding, many of which contradict popular opinion. I suggest you follow a rule that Stucco Technology Institute (STI) instructors use when instructing student EIFS inspectors: ”Do not form preconceived opinions. The structure will tell you what the cause of the problem is, if you heed the signs.” STI has trained over 1500 EIFS inspectors and applicators.
A. CLADDING AND THE BUILDING ENVELOPE
EIFS and other forms of cladding do not normally fail. That is to say, water does not penetrate directly through the surface of the cladding. It penetrates the building envelope. The envelope includes secondary moisture barriers such as felt paper and Tyvek, flashing, and the primary moisture barrier which includes windows, doors, cladding and sealants. The points of water intrusion are identical in virt
ually every condo or residential project I inspect. The windows were not flashed, and leaked at the lower corners, kick out or diverter flashing was not installed at roof/wall intersections, allowing roof run off to get behind the cladding, and decks were not properly flashed. If those conditions did not exist, there would be no water intrusion.
Here are some things for you to think about:
1. Few of the general contractors, building residential or light commercial, including condos and apartments in this country have been trained in the basics of moisture intrusion prevention. They rely mainly on their subcontractors to install the cladding components according to manufacturer specifications.
2. EIFS is not a subject taught to student engineers or architects.
3. The local government paid building inspector, contrary to popular belief, is not responsible for assuring the water tightness of the building envelope. Much of their time is spent inspecting work completed by licensed contractors, yet, only a handful of the inspectors are required to pass any type license exams, to test their knowledge. Local building departments, in their defense, have the same problem most construction companies have; finding skilled employees.
4. There are lots of condos, apartments and residential projects under construction, which do not have EIFS, but lack a viable secondary moisture barrier and flashing, and will experience typical moisture intrusion problems. I just recently opened a wall on a house, completed 6 years ago, which is clad with stone veneer, and is experiencing moisture intrusion, wood rot, and mold growth.
5. All wood frame construction shrinks. The wood dries and the building weight compresses cross grain members. A two story building will shrink ¼ to ½ inch in one year. This means all of the structural framing gets smaller, but the plywood or OSB does not shrink. The entire weight of the building transfers to the sheathing, and eventually the sheathing buckles at the second floor line, thus the bulges you can see at the second floor line, so common to wood frame construction. There should be a one-inch gap in the sheathing horizontally at the floor line, to allow for the compression. The compression joint then must be installed in the cladding, at the floor line, to absorb the shrinkage or there is potential for a breach in the building envelope.
6. Residential EIFS, in the 1990’s, was installed for less than $4.00 sq. ft., while commercial EIFS cost about $6.00 sq. ft. Material price was the same for both. The $2.00 savings in residential, came from the omission of flashing and sealants, and disregard for manufacturer specifications and application instructions. Why did this happen? Because general contractors were too busy looking at their bottom line when awarding EIFS contracts. They went with the fly-by nighter’s. Plain and simple.
7. The residential building envelope is usually flawed. If it can leak, it will leak. All EIFS should be inspected by a trained inspector during all phases of application. Further, all residential construction should have a secondary moisture barrier. Or better yet, never put EIFS on wood. Use Durock.
B. BAD ADVICE?There are only three of 1,400+ projects, in my 15 years experience, where I was involved in some capacity, which EIFS had to be totally removed. Most EIFS clad structures do not have to be stripped, at least from a technical standpoint. I hardly ever hear of complete tear-off with EIFS.
Here in Hampton Roads, a local architect was quoted in the Virginian Pilot, as saying he has seen at least seven EIFS clad communities struggle with water damage behind EIFS. One of those projects, where he recommended the EIFS be completely stripped and the buildings clad with cement board siding, was photo documented during the envelope demolition. As fate would have it, Daniel Perez, STI Chairman, was inspecting a project directly across the street while the EIFS was being ripped off. Daniel is a master estimator and capacity assessor. So, while inspecting the repair progress of his project, he photographed the EIFS rip off across the street. Daniel stated: “ 95 % of the sheathing on Gaviotas Villas had no moisture damage, and there was no rationalization to rip it off. The only moisture damage was at poor quality leaking windows, below improperly flashed decks, and where diverter flashing at the roof/wall intersection was missing.” Do not rip off your EIFS without substantial forensic investigation.
C. HOMEOWNER GUIDE TO INSPECTING EIFS
An epigrammatic inspection can alert you to potential trouble spots.
1. Check roof / wall intersections to see if an KO flashing has been installed to divert the flow of water away from the vertical wall.
2. Check the lower corners of windows for any gaps in the corner miters, and probe the sealant to determine if is still flexible.
3. Look for any bulges at the second floor line.
4. Carefully check your deck, if it is wood frame and attached to the house. There should be visible flashing and no sign of wood rot.
5. EIFS should not be installed below grade, so when replacing mulch, first remove the old mulch.
6. If you suspect a problem, go to
http://www.eifs101.bravehost.com/ . 85% of all remediation costs less than $1,500, and is usually a maintenance issue. Keep in mind, water intrusion is cumulative. The longer water penetrates the building envelope, the greater the potential damage. If only everyone had used cement board instead of plywood. But I digress.
D. MOISTURE READINGSMoisture content of wood must exceed 19.5% for the algae, which causes wood rot, to exist. Kiln dried lumber is dried to 19%, prior to shipment to lumber yards. There are so many references to moisture content of wood by so many scientists, testing labs and agencies, anyone who states a 10% moisture reading in wood or OSB sheathing should be considered an elevated reading, is simply making up the rules and completely disregarding an army of highly trained experts. Likewise, any inspector or consultant who states any moisture reading in any type of wood, exceeds 40%, has their moisture meter probes submerged in a glass of water, or is using the wrong equipment. Without a doubt, this individual is not a qualified moisture analyst. Most grades of construction lumber and sheathing cannot absorb more than 30 –35% moisture before reaching total saturation. The harder the species, the lower the saturation point. Why? The wood fibers take up the rest of the space. There is simply no more room for water without removing the wood fibers.
E. NEW CONSTRUCTIONEIFS was the product of choice in high end residential construction during most of the '90’s, because of the dynamic design potential and curb appeal. The problems learned about EIFS in residential construction, have been addressed in the STI Integrity Program. The STI Integrity Program addresses potential oversights of all responsible parties in the EIFS cladding chain. Manufacturers in this program are required to issue a 10-year labor and material warranty. Applicators must complete certification training, be sponsored by an STI registered manufacturer, sign a three year blanket labor warranty, and then will qualify for liability insurance underwritten by Lloyd’s. All projects must be inspected by an STI certified Quality Control Consultant, paid by the STI Loss Prevention agents, which helps avoid complicity. All parties must sign a binding arbitration clause to qualify for the Integrity Program. This program is not designed to protect the applicator or manufacturer. It is designed to protect the building owner.
Beware of the engineer, architect, consultant or contractor who says you must rip off all of the EIFS. If you do need to fix your EIFS home or condo, be absolutely certain the contractor is insured, and has a current valid contractor license. Good construction is a must to protect home and building owners.
F. PRIMARY AND SECONDARY MOISTURE BARRIERS
Tyvek, felt paper or liquid applied membranes are all components of the secondary moisture barrier. Add flashing, windows, doors, and the walls should be able to shed water without any moisture reaching the sheathing or framing. Next comes the cladding and caulking (sealant).
My test equipment of choice for the secondary moisture barrier is a garden hose. If the secondary barrier leaks, it is a waste of time to put in on at all, which, by the way, is the reason many cladding installers don’t bother with it. On the other hand, if it performs as it should, shedding all water, then it really doesn’t matter what cladding is used, the sheathing and structure are protected.
The only work left, is to properly install the primary moisture barrier according to details and specifications. If this is done correctly, the secondary moisture barrier remains a dormant backup to wear and tear of the cladding. All cladding does need some sealant, depending on the cladding used. Never use acrylic caulking on the exterior. It has an anticipated life of less than two years, and a 10% movement capability. Use only urethane or silicone sealants. My material of choice is Dow 790, which is a pure silicone, with +100% and –50% movement capability. The anticipated life is 20+ years.
G. QUALITY OF CONSTRUCTION1. Many cladding contractors sub contract their work to “piece work” contractors. This means the contractor you hired doesn’t actually do the work, but pays another crew by the square foot, to install the cladding. They are often unsupervised.
2. Many cities and towns have set policy requiring an independent third party EIFS inspector to sign off on a project before they will issue a certificate of occupancy.
3. Residential contractors may lack on site supervision of sub contractors, or have inexperienced supervision. But then again most contractors don’t know the first thing about installing EIFS correctly.
H. CONCLUSIONSIf your car starts pinging and ponging, do you take it to a third party auto consultant? I hope not. You call a knowledgeable mechanic, and get the problem fixed. When your home leaks, it is a warning sign of the problem. Something in the building envelope is usually the problem. If you have leaks in the ceiling, it may be the roofing, but it may also be flashing or clogged gutters.
Treat your home the same way your doctor treats your medical ailments. Symptoms lead to causes, and causes are what must be treated. Don’t waste your time treating the symptom, it will just mask the core cause and could lead to more severe problems.
If you own an EIFS home, don’t panic. If you plan to sell your EIFS home, get it inspected prior to putting it on the market, as any professional real estate salesman would suggest. If you plan to buy an EIFS home, require an inspection as a condition of purchase.
The EIFS industry perception in the ‘90’s was negative. But it was very similar to the problems experienced by the rubber roof industry in the ‘80’s. Their solution was to require independent certified roof inspectors to sign off on every installation, and the problems disappeared.
EIFS clad homes, buildings and condos can be repaired at a fraction of the cost of complete removal. Community and condo boards of directors can be held accountable for meeting their fiduciary responsibilities. They must accumulate a reasonable amount of funds to cover the costs of long term as well as short-term maintenance. If you do choose to sit on a board, be sure E & O and liability insurance is in place for directors and officers. There are many competent attorneys specializing in just this sort of situation. Check with your real estate professional for referrals.
If your association is responsible for more than 4 units, hire a management company, who can guide you through the procedures and keep you out of trouble.
Many of the buildings you drive by each day, are clad with EIFS. Hotels, motels, malls, churches, office buildings, most of Las Vegas, and some of the largest and most prestigious homes are all EIFS. If it is particularly fancy, has a lot of architectural detail, large monolithic surfaces, it is probably EIFS. It is one of the most widely used claddings in the commercial market. They do not have the typical home or condo owner problems, because the commercial projects generally have lots of supervision. The same could be said about the residential market, if every project got an independent inspection.
Finally, do not blame the EIFS, blame the building sheathing, then maybe you won’t get ripped off.